Monday 7 December 2009
Final thoughts and reflection
The group worked very well together in most aspects and the progress that we made weekly seemed amazing, even as I look back now.
The primary aspect that made the project so successful was communication. Right from the beginning, we agreed on a size scale to use, and this made it very easy later on when the different models were brought together. We met weekly to discuss what we had achieved over the week and set ourselves targets for the following week's meeting. Another key to the group's success was the fact that we managed to complete the main modelling aspect so quickly. This then gave the group more time to work on the animation and lighting/movie segments.
As Stuart lives quite a way from the University campus, it seemed more ideal that we contacted him via e-mail, and met just once a week. The rest of the group met every couple of days.
The workload was shared evenly. I took on the main model, Tom took the left section, Richard took the wheel and individual arm and Stuart took the right section and environment. It was basically a process where once someone had finished working on their section, they then moved on to something else that could be done. For example, after I completed my modelling aspect, I then moved on to creating some environment (ie snow and sky scenery). I also worked with other members to arrange the lighting and to create the final movie. This consisted mainly of arranging the various cameras into the right positions and making sure that the cameras displayed the scenes as we required.
Unlike many groups that have done projects like this before, the team worked really well together. Something that amazed me was the way the group got on with the work and never argued. We all contributed ideas, and then went with whatever the group agreed was the best option.
Throughout this project, I have yet again learnt so many new skills. Having never used 3DS Max before the face project, I have really been thrown into the deep end of modelling. The only way that I overcame my lack of experience was to sit and work through tutorials and spend hour upon hour learning how the software works. I have learnt so much. The techniques that I have acquired have proved really useful. Things like using the Boolean tool, adding and altering textures to display bump maps and anistrophic settings, lighting settings and key frame animations are to name but a few techniques that I have learnt.
The animation was relatively difficult to get right. Key frames seem to have a mind of their own. I had great difficulty when I grouped objects, animated them, then when I went to ungroup them, they distorted and the animation did not work as I required. The animation was also very fiddly, and typical of me (being OCD) I had to make sure that it was 100% correct.
I was initially concerned with creating the lighting effects and also the movie aspect.
However, working with the rest of the team, I soon learnt how everything works, and am now quite experienced in these areas. Creating a movie is a lot simpler than I thought. It is really just a case of placing the camera in the correct place, then moving through the key frames, making sure that it shows in the view port what you want to display.
At the beginning of the project, the group analysed everyone's strengths and weaknesses. This was vital, as it enabled us to work out who would do what within the project, making sure that everyone worked in areas where they were best suited. However, this did not stop us from learning new skills because with all 3d modelling, there is always something new to learn.
Looking back over the entire project from day one, I can not believe that we have created the model that we have. Our model resembles very closely to the original model. There are no particular areas that I am not proud of. We have now created a movie which provides an educational perspective (Commentary at the beginning) and a short film showing how the model works. I feel that this really is something that the museum could benefit from, which was our initial aim from the beginning.
If I were to go back to the beginning and do this project again, I would keep most things the same, although there are a few things that I would change.
Firstly, before anything else, I would arrange with the group exactly what our aims are and what we want to achieve from this project. Secondly, I would try to meet with the team more. And thirdly, I would try to ensure that the group used the same textures throughout the model, as sometimes working on your own, people tend to use their own textures which do not follow suit to the rest of the model.
However, I feel that the team worked really well together and I am extremely proud of the product that we produced. Maybe one day I will return to the museum and see our animated model/movie on display....
Wednesday 2 December 2009
Environment

(Outhouse with sky)
Applying a snow texture to the plane was what I did next. I increased the bump map to 117 so that the snow had some contours. I then placed the steam pump into the outhouse ready for it to be filmed using cameras.

(Outhouse with snow and sky included)
Finally, I decided to add some lighting effects alongside Richard. We placed a spotlight onto the gauge where the first movie will start from. We also increased the intensity of the light within the outhouse so that the model could be seen clearly when animated. Some external lighting was also included so that the outhouse could be seen in greater detail.
Tuesday 1 December 2009
Updated animation
We have now completed the animation of the model itself, which lasts for approximately 700 frames. Previews of the first 250 frames are shown below:
The gauge which Tom has been working on also needed to be animated. So, as I have had a lot of practice with animation now, I decided to continue with animating the gauge.
To do this, I created a new gauge arm which resembled the red one that Tom created, and coloured the new one in black. This could then be animated.
I then turned the key frame record on, and started to move the arm around accordingly. I encountered many problems, worst of which was the fact the the gauge was joined to the main model, and when I ungrouped it, the previous animation became corrupt. So, I had to animate the arm on the gauge at an angle, which meant that when I moved the arm to be animated, I had to correct it on all axis. This took a lot longer than I intended. I moved the arm up to around the 15lbs mark, and then moved it up and down a few times so that it gave the impression that it was juddering. I then gradually increased the arm, and half way made the increment even faster as the wheel then slowly comes into motion. A preview of this can seen below:
Wednesday 25 November 2009
Additional end joint
Reflection from meeting (19/10/09)
The interim presentation that we gave went smoothly and the general response from other students was positive, particularly when we showed the animation that I have been working on.
The group are now starting to look further than the animation by looking at the environmental aspects, with particular attention towards the outhouse and surrounding area. Stuart has made a start on creating the outhouse, and I shall be working alongside him to complete it. Hopefully, the model with then be placed inside and animated so that the camera 'flys' through a window or door and into the outhouse, to then show the model in motion.
We have set ourselves manageable targets for this week that we will be working on. My main targets are to complete all the animation for the arms and also to texture the model. Once added with Richards fly wheel and arm, there is not a great deal left to do with regards to animating the model. We will then be able to start focusing more towards the post production elements.
A deadline has been set for 6th December, where we aim to finish the model and animation aspects, with the intentions of using the last week to finalise and prepare for the presentation to Terry Bradley (Voluntary Trustee of the Museum of Power).
Model in animation
Thursday 19 November 2009
Preparing for animation and textures

.jpg)
(Base after the section had been removed)
To make the model look even more realistic, I decided to start adding a few textures to see how the model looked once they were applied. I have added a red texture created in Photoshop onto the arms, and will be adding further textures at a later date. Changing the parameters, I was able to create an effect on the texture that made it look more metalic. I changed the texture to anistropic in the basic perameters and altered the specular highlight to create a reflection from any light that is cast onto it. The settings are shown below:
The image below shows the arms with textures applied:
The same technique was used for the metal caps and the ring around the front arm:

Friday 13 November 2009
Reflection from meeting (12/11/09)

I was initially very pleased with how the model was coming along. The size scale that everyone used matched correctly, and there were no aspects of the model that didn't fit together. As you can see from above, there is still quite a lot of work to be done on the modeling before we can really attack the textures and animation. Now that I had completed my modeling aspect, the group decided that it would be a good idea for me to make the initial start on the animation, alongside Richard. The group then agreed that Stuart could work on the environment where the machine will be situated within. Tom would then work on the story board, and develop a plan of action for the short movie that we will eventually make.
Our aim for next week is to bring all of the final modeling aspects together, and create one final model. We will then all work from the same file, where Richard and myself will create the animation and Tom and Stuart will work on textures, lighting and the environment.
Tuesday 10 November 2009
Final modeling stage



(Additional detail to the end arcs)
Just when I thought that the model was complete, I noticed that there was a bolt and two triangles at either end of the model, attached to the end arcs. So, I cloned a bolt, and placed it in the correct position above. I then used the lines spline tool to draw a triangle, and extruded it in the usual way with a slight chamfer modification. I then cloned this object and placed it on the other side of the bolt. Cloning these three objects, I then moved a copy of them down to the other end of the model.
The modeling aspect of this assignment, for me, is now virtually complete, although I am sure that there will inevitably be some additional work required. I will be adding the adequate textures to the model, as at present, the modeled aspects are only coloured rather than textured. This will be done alongside the other members of the group. We will then collate all of our created models on Thursday 12th November, where we will hopefully have a completed model. Once textures have been applied, we will then animate the model using the videos that we took. Lighting and video caption will then be adhered to in order to have a final movie that we will then show to the museum.
Below are a selection of images of the finished model (without textures) from various angles:
(Final image of model)

(End view of model)

(Rear view of model)
(Diagonal rear view of model)
Friday 6 November 2009
Arm number 2


(Close-up of additional detail)
When I duplicated the arm, I added another metal cap object onto it, as the original source photo shows.
Using the clone tool, I made another copy of the end base plate and nuts/bolts that were attached to it. The scale tool then enabled me to make this a lot more smaller, and I rotated the object 180 degrees. As you can see above, I then placed this at the end of the 2nd arm, and attached the two together. This is now ready for when Tom has finished modeling his section, so that we can connect the two objects together (Tom's model and mine).
Reflection from meeting (29/10/09)
I feel that the team are all very strong at creating models in 3D Studio Max and I am feeling positive about our approach to animation when that comes along.
Although we have been only working on the modeling aspect for one week, the team are getting very close to starting the animation aspect. Because of this, we decided to set the next deadline as Thursday 12th November, where we will start to create some animation. As I have finished the main structure of the base, the rest of the members took a copy of this. We did this so that the model would all come together and connect at the correct places once everyone had finished the separate sections.
To share the workload, we decided that every week a new member of the team would write the minutes to each meeting. I wrote the minutes to week one, Stuart is doing the second week and Richard and Tom will be doing weeks three and four.
Next week we will be merging all of our model to create the final product. From there, we will then be applying textures and animating the model. Group discussion then led onto incorporating various sounds and even having a voice over, explaining about the model and what it was used for etc.
Wednesday 4 November 2009
Creating the animated arm (Part 2)




(Additional detail added to the top of the wheel)
Using the metal cap that Richard created, I placed this on top of a chamfered box slightly to the side of the wheel. We believe that these metal caps were used to pour oil into, in order to keep the machine well lubricated. I then created another two boxes similar to the first one, where I then placed them on top of the wheel. Using the clone tool, I then positioned a nut to the left side of the boxes and a bolt head to the right side of the boxes. This then gave the impression that the two boxes were held together by this bolt. The difficult part of this section was sizing the metal cap that Richard created. When I merged this with my document, it was far larger than what I required. As such, I then re-scaled the object so that it was a suitable size.

(Friction plate)
To create the friction plate, I simply drew a chamfer box and set the level so that it was only barely chamfered. As this made the plate look slightly rigid around the edge, I decided to add a Turbo smooth to this object, so that when it rendered it had a smooth surrounding.
Creating the animated arm
To create the arm shown above, I first created a standard chamfered box, making sure that the fillet level was correct to match the rest of the model. Converting this to an editable poly, I then selected all of the end vertices on the right hand side and used the scale tool to pull them slightly closer to each other. This in turn made the end of the arm slightly narrower. I then scaled the rest of the arm so that it matched my original source photograph.


Tuesday 3 November 2009
Initial stage of the first animated object
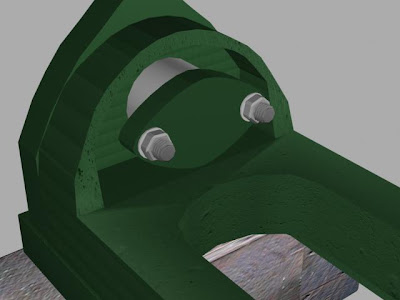
(Nuts and bolts cloned onto the end base plate)
Now that the nuts and bolts are created, I decided to clone them for the end base plate. So, I selected the bolt, washer and one of the nuts and right clicked. Selecting the clone tool and choosing 'copy', I then created a copy of the objects. I then rotated them and dragged them onto the end base plate. As the nut, bolt and washer were a little small, I selected them all and scaled them to make them slightly larger. This then gave me an exact representation of my original source photo.
(Capsule created and modified)
I decided to create the object as shown above. It will become clear in the next stage why I decided to make this. So, first I used the 'capsule' tool to create a standard horizontal capsule. I then converted this to an editable poly and selected the vertices option. Highlighting the two middle vertical rows of vertices, I then dragged them in towards each other using the scale tool, then used the move tool to place them slightly higher. This then left me with this 'jelly bean' shape.
(Cylinder after the boolean tool)
As can be seen from the image above, I first created a chamfer cylinder. Cloning the 'jelly bean' shape that I created in the last stage, I then positioned them in the correct place where they have now removed a chunk out of the cylinder. I then selected the cylinder, and used the Boolean tool, choosing one of the 'jelly bean' shapes as the operand B. I repeated this process, which then left me with two sections missing, which are in the shape of a jelly bean.
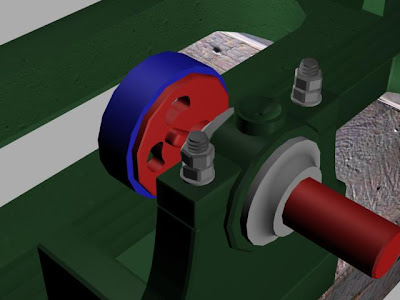
(Tube created around the cylinder)
I have now started the creation of the first object that will be animated. This is the moving arm at the front of the pump. Creating a standard tube around the cylinder that I created has enabled me to continue with the rest of the front arm, which I shall do so within the next section.
Yet more work on the front panel

(The result of the two objects after the Boolean modifier)
As shown above, the effect is yet again very promising. I am very pleased with the replication of this front panel now and feel that it looks similar to the original image that I am working from. The cylinder that has been added at the front is a simple chamfered cylinder with the correct size and fillet level applied.
(NGon created for the nut)
Noticing that there are quite a lot of nuts and bolts within this model, I felt that it was a good time to start creating some. I also knew that once I had created one, I would be able to replicate it many times for most of the other nuts and bolts. So, I started by using the NGon tool within the splines modifier panel. This then provided me with the 6 sided shape as shown above. I then used the extrude tool, which gave me a 3 dimensional object. Converting this to an editable poly and selecting all of the edges, I then altered the chamfer level so that they became very rounded, rather than square. This then created the nuts shown below, and once bolts are placed within these nuts, it will then look far more realistic. Washers (Simple, very thin cylinders) have been placed below the nuts to add to the effect and to also match the original source image. I am now able to clone this object as and when I require more.

Adding detail to the model

(With Texture)
Adding the dark green texture that I have used for the rest of the model made the cylinder and rectangle look a lot more realistic in resembling my original source image.
(Cylinder and Torus)
As with many models in 3D Studio Max, there are many ways of creating them. For the gold colour section on the front, I decided that the best method here would be to create a cylinder and a torus, then use the Boolean too. So, once both objects were created I selected the cylinder. Using the Boolean tool in the compound objects section, I then selected the 'pick operand B' command, and chose the Torus. This then deleted the Torus and left me with a cylinder with the perimeter cut away.

(Cylinder after the torus has been removed)
As can be seen from above, the outcome is very effective. The Torus has been removed by the Boolean tool, and the cylinder has a nice indentation all around the edge. It took me a couple of attempts to get the Torus in the right position, primarily because the depth was quite hard to judge. Through trial and error, I managed to overcome this issue and was left with an object very similar to that of the one in my source photo.
(End base plate)
Behind the end base plate is a simple cylinder object. Although it is quite difficult to see this shape from the original source photo, I know that it is a cylinder because I remember this from when we visited the museum, and I also used some of our other photo's to confirm that this was in fact the shape behind the end base plate. To create the base plate itself, I used the lines spline tool. Within the front view, I drew a shape that was similar to the shape in the source photo. Using smooth in both the initial type and drag type within the creation method parameter, I was able to get a smooth edge around the object, rather than one that was rigid and too square. Converting it to an editable poly, selecting the polygon, then extruding it to the required length gave me some depth to the object. Finally, I rotated the object and positioned it to where it needed to go. There was some slight alterations that needed to be made to the size of it, but this was really just a finishing touch to get it to the perfect size as shown in my main source photograph.
Monday 2 November 2009
Arcs at either end

Main structure of the model
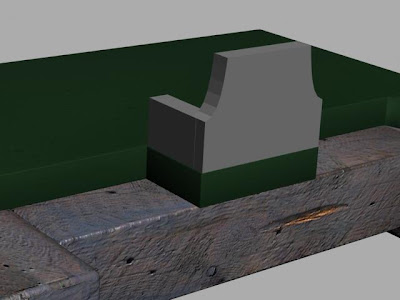
(Object mirrored and sides added)
Now that the shape had been created, I then used the mirror tool to create a reflection of this object, making sure that the mirror axis was set to 'X' and the offset was 8.149cm (copy). This is shown below. I then created two standard rectangles either side, making sure that they were the same depth as the first object I created, and the correct length. The last task for me to do was to add the dark green texture that I created in Photoshop, the same as I did for the main base plate.
(Settings used for the mirror tool command)

(Additional detail for the nut and bolt)
At this stage, I noticed that there was further detail required for the bolt that holds the machine down onto the wooden blocks. As such, I created a cylinder that was very thin, and placed this below the bolt that I had created, lifting the bolt up very slightly so that it fitted underneath. I then scaled this cylinder down so that it was the correct size according to the source image. I was pleased with this outcome, as it looks far more realistic now witht the washer included.
(Left view of the model)
There were many ways that I could go about creating the main section of the model. I could have created it in many sections, but the way that I thought would be most effective, was to create the main object, then us the boolean tool to remove sections. So, as you can see from above, I used the line tool to draw the side profile of the object. I then closed the splines. Using the extrude tool, I was then able to create a long object. This was then scaled to fit the entire length of the metal base:
(Effect of the extrude tool)
As you can see from the image above, the extrude tool has allowed me to have the arc shape that I created in the left view to stretch across the entire base. At this stage, I realised that there was a slight problem with this. Where I have created the object using the line tool, the arc shape is not very smooth, and this may cause me trouble late on, particularly when texture is added. I shall address this problem later on with Tom, when the group come together towards the final stages to finalise textures and mapping.
(Box created ready to use the Boolean tool)
First, I scaled the arc shaped box inwards slightly, as I noticed that there were other slightly larger arcs at either end.The boolean tool is probably the most used tool within 3D Studio Max. I certainly seem to use it more than any other tool. So, I created a box. This was then converted to an editable poly, where I pulled the bottom vertices of the box in slightly so that the extruded arc would not be completely vertical at the edges, but have a slight slant to them. Selecting the arc object, I once again chose the boolean tool, and picked the box I had just created as the 'operand B'.
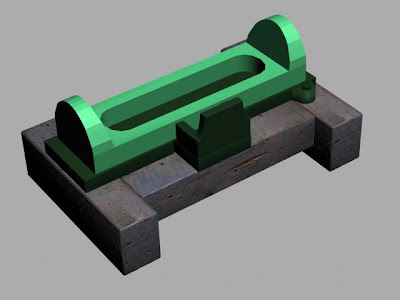
(After the Boolean tool had been applied)
The boolean tool left me with the image above. However, I have also used the boolean tool again on a chamfered box so that the arc shaped object went right through to the base unit.
(Removing the bottom panel)
Looking again at my original source image, I noticed that the middle of the machine and base was completely empty, and you can see right through to the floor when looking from a birds-eye view. So, I created another chamfered box onto the metallic base, and used the boolean tool to remove a segment from the base. This then left me with the image below, where there is a large gap with no fill:
(Image showing a complete gap in the middle of the object)
As with every section, I applied the required material. In this case, it was the dark green material/texture that I originally created in Photoshop.
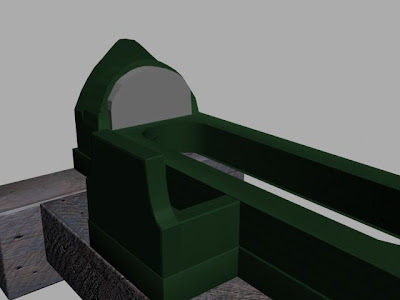
(Creating the indentation at the ends)
At either end, there are indentations that go into the arcs. These are important, because they then make the arcs perfectly vertical within the indentation rather than being slanted as I created them. I will need the ends to be vertical later on because there will be objects that will need to lay flush to a vertical object.
So, I created a smaller arc to the existing one, the same way as I did previously. Using the clone tool, I was able to replicate this arc at the other end of the model. I then selected the main model object, and used the Boolean tool to remove the arc object and a segment within the main model. Repeating this at the opposite end of the model gave me the required indentation.